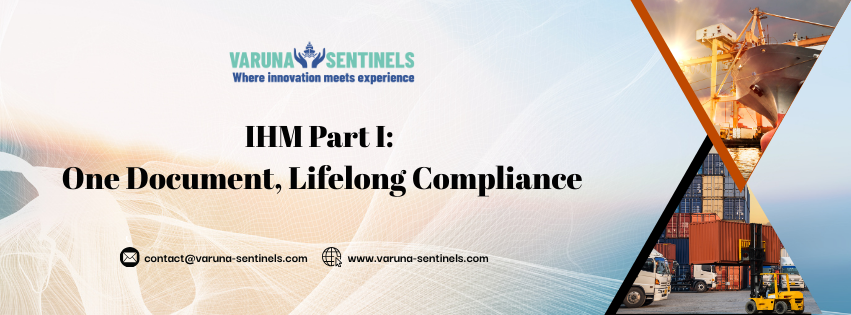
You got your Inventory of Hazardous Materials (IHM) ready.
You passed your inspection.
You think you’re done? Not quite.
Maintaining IHM isn’t just a one-time task—it’s a continuous responsibility. In the world of shipping, regulatory compliance doesn’t stop at certification. And when it comes to the IHM, keeping it up to date is just as important as getting certified in the first place.
Let’s break it down—in plain English, no legal jargon.
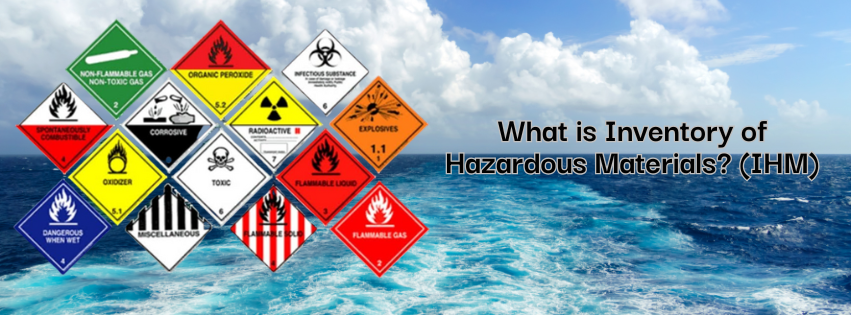
Think of the IHM as your vessel’s “hazardous materials report card.”
It identifies all dangerous substances (like asbestos, PCBs, mercury, etc.) present in your ship’s structure or equipment.
It consists of three parts:
- Part I –Structure & equipment (must be kept updated while the ship is in service 🛳️)
- Part II –Operationally generated waste
- Part III –Stores
👉 For vessels in operation, Part I must always be current and updated.
🔍 Why Should You Care?
Because it’s the law—and ignoring it can lead to serious consequences.
Under the EU Ship Recycling Regulation (EU SRR) and the Hong Kong Convention (HKC):
- Ships without an updated IHM may be detained at ports
- You could be denied access to EU ports
- Fines, delays, and damage to your company’s reputation can follow
What Does “Maintaining IHM” Actually Mean?
Here’s the short version:
Every time you purchase, install, or replace something on your vessel, you need to:
- Check if it contains hazardous materials
- Request a Material Declaration (MD)
- Get a Supplier Declaration of Conformity (SDoC)
- Update your IHM records accordingly
It’s not just paperwork—it’s proof that your vessel is safe, compliant, and environmentally responsible.
Real-Life Example
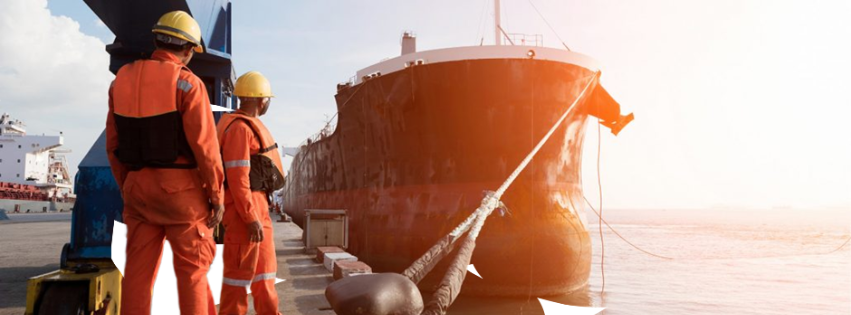
Let’s say you purchase a new generator.
- If it comes with MD & SDoC—you’re compliant!
- If it doesn’t—you’ve just added a potentially hazardous item without documentation, which could lead to compliance issues.
This is one of the most common reasons vessels fail IHM inspections—especially during urgent or last-minute purchases.
Keep an IHM Logbook – Your Secret Weapon
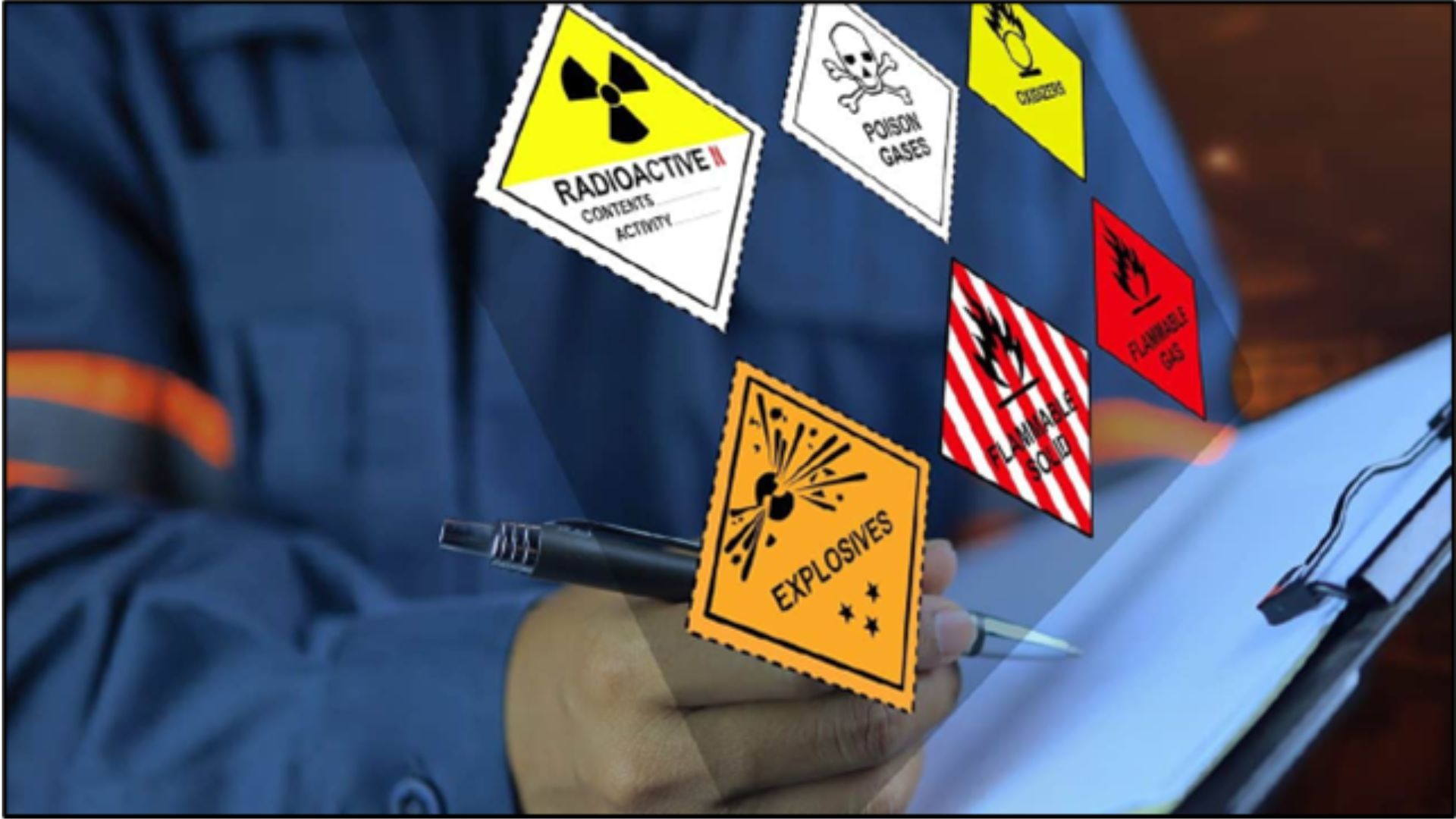
Maintain a simple logbook that tracks:
- What items were added or removed
- When they were installed
- MD/SDoC status (received or not)
- Who was responsible (crew/office)
- Any pending issues or follow-ups
- Any pending issues or follow-ups
During Port State Control (PSC) inspections, this logbook can help prove your compliance and avoid detention.
Go Digital – Simplify the Process
Let’s be honest—tracking MDs and SDoCs through emails or spreadsheets isn’t ideal.
That’s why digital tools like:
- VSIMS by Varuna Sentinels B.V.
- ClassNK IHM Portal
- GreenDocs by Green Instruments
...can streamline your IHM maintenance by automating document collection, sending alerts, and syncing with your PMS.
Less manual work. More control.
Common Pitfalls to Avoid
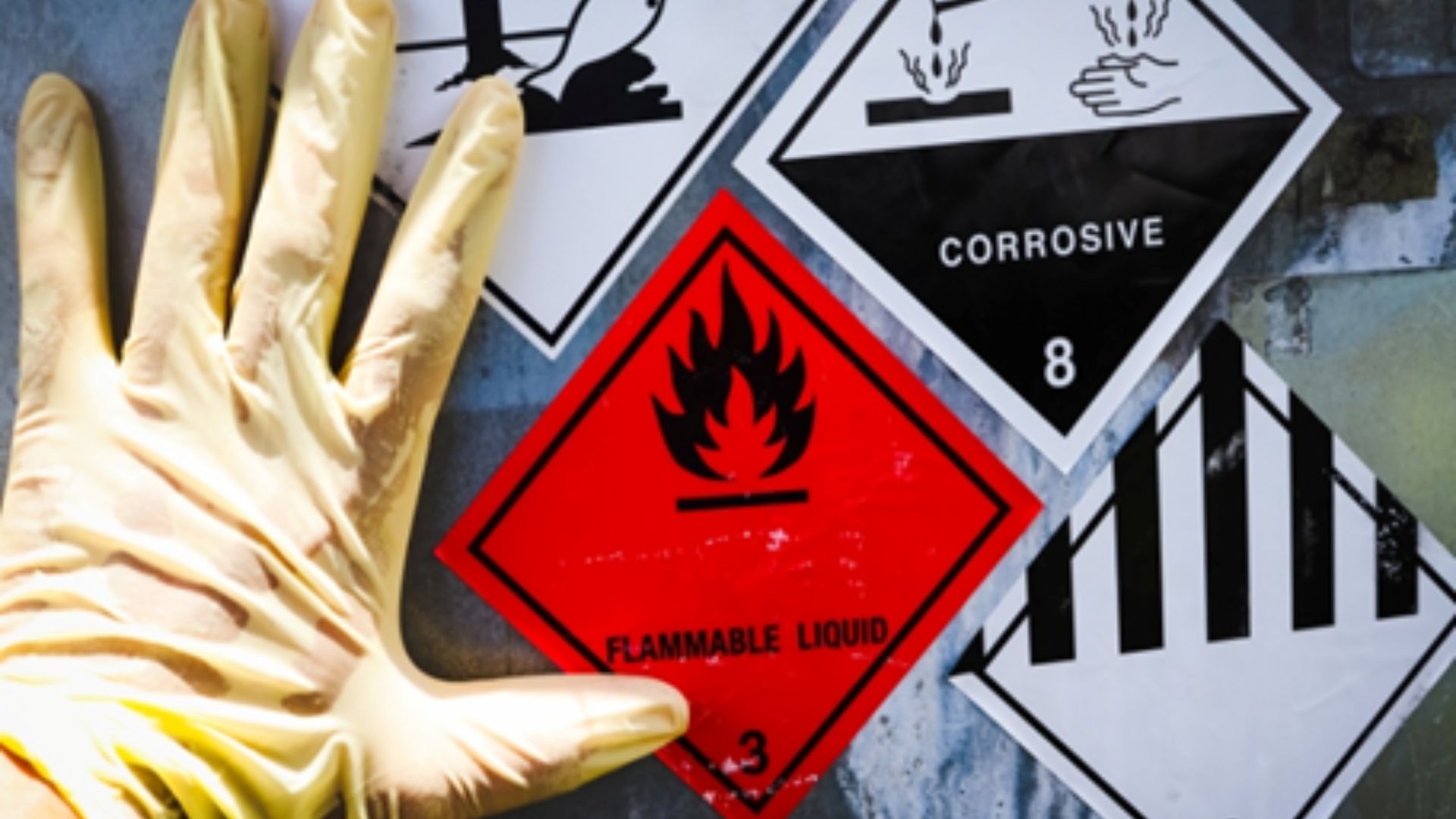
- Purchasing from non-compliant suppliers
- Skipping MD/SDoC requests for urgent orders
- Failing to update IHM after drydock or repairs
- Not assigning clear responsibility for IHM management
Pro Tips to Stay Ahead
- Include IHM clauses in all supplier agreements
- Train your purchasing team to always request MDs and SDoCs
- Review your IHM quarterly
- Use digital tools instead of spreadsheets
- Keep backup documents safely stored (cloud or secure drive)
Bottom Line: Compliance = Responsibility
Maintaining your IHM shows that your company values:
- Crew safety
- Environmental protection
- International compliance
- Smooth port operations
Need Help?
Varuna Sentinels B.V. helps global fleet operators simplify IHM compliance with tools, support, and automation.
Reach out to us if you want to:
- Simplify IHM maintenance
- Prevent port issues
- Stay ahead of new regulations
Let’s make IHM compliance simple and stress-free.